CalRecycle
California has the most aggressive and successful recycling law in the country. The California Department of Resource Recycling and Recovery (CalRecycle), with an annual budget of $1.5 Billion, is responsible for administering the current law. Despite attempts to incentivize the public with bottle redemption centers, the average consumer still places their glass in curb-side recycling bins. Curb-side haulers handle the majority of the glass which is then processed in single stream MRFs (material recycling facilities) and sent on to a glass processor.
Post-consumer materials from single stream curbside recycling programs, including glass, are collected and transported to a MRF for sorting. Only the larger mix color, broken glass goes to the glass processor. All fines or unsorted glasses, collected at both the glass processor or the MRF are transported to a landfill for disposal. 75% of all glass that enters the waste system in the United States ends up in landfills. That’s 110,000,000 glass bottles going into US landfills every single day.
CalRecycle awarded SiONEER a $3.0 Million Greenhouse Gas Reduction Grant based on SiONEER’s unique ability to process glass fines and the GHG saving that results from the use of SiONEER pozzolan in concrete. $2.4M of these funds are eligible to fund a portion of the equipment that will be used in the facility.
Greenhouse Gas Reduction
The State of California has spent billions of dollars in an effort to reduce GHG. As a result of the recently awarded CalRecycle Greenhouse Grant, SiONEER was required to document and prove the amount of GHG savings that would be associated with using the SiONEER pozzolan product in concrete.
These calculations were reviewed and verified by the California Air Resource Board. The net GHG emission reductions when comparing one metric ton of SiONEER Glass Pozzolan to one ton of portland cement can be calculated to be:
GHG [net] = 0.88 − 0.046 = 0.834
Further, based on the projected production of 100,000 tons of SiONEER Glass Pozzolan per year, the net impact will be a GHG emission reduction of 83,400 tons of MTCO2e annually.
SiONEER Glass Pozzolan Manufacturing Process
According to research competed by leading scientists and engineers who specialize in sustainability and innovative concrete materials, the SiONEER Glass Pozzolan (SGP) manufacturing processes “… will result in permanent and measurable reduction in greenhouse gas (GHG) emissions from the handling and landfilling of mixed broken glass by diverting this waste material from the landfill and recycling it into a glass pozzolan for use as a cement replacement in concrete products.”
The production of portland cement, which is the most commonly used cement in the world, releases approximately 0.88 tons of CO2 per ton of cement produced, and is reported to be responsible for 5-8% of global anthropogenic carbon emissions annually. By replacing portions of the portland cement in concrete with a glass pozzolan, significant GHG emissions can be achieved.
What makes the SGP manufacturing process unique is that it will process the MRF glass as above, and also refine the fines and other unsorted glass into valuable commodities. The glass initially destined for the landfill can now be transported to the nearby SiONEER CleanGlass Plant, where it will undergo an initial grinding process, a sanitization treatment process, a drying process, and a final grind. The resulting material will be a fine glass powder, which can be transported to a concrete manufacturer for use as a pozzolanic portland cement replacement.
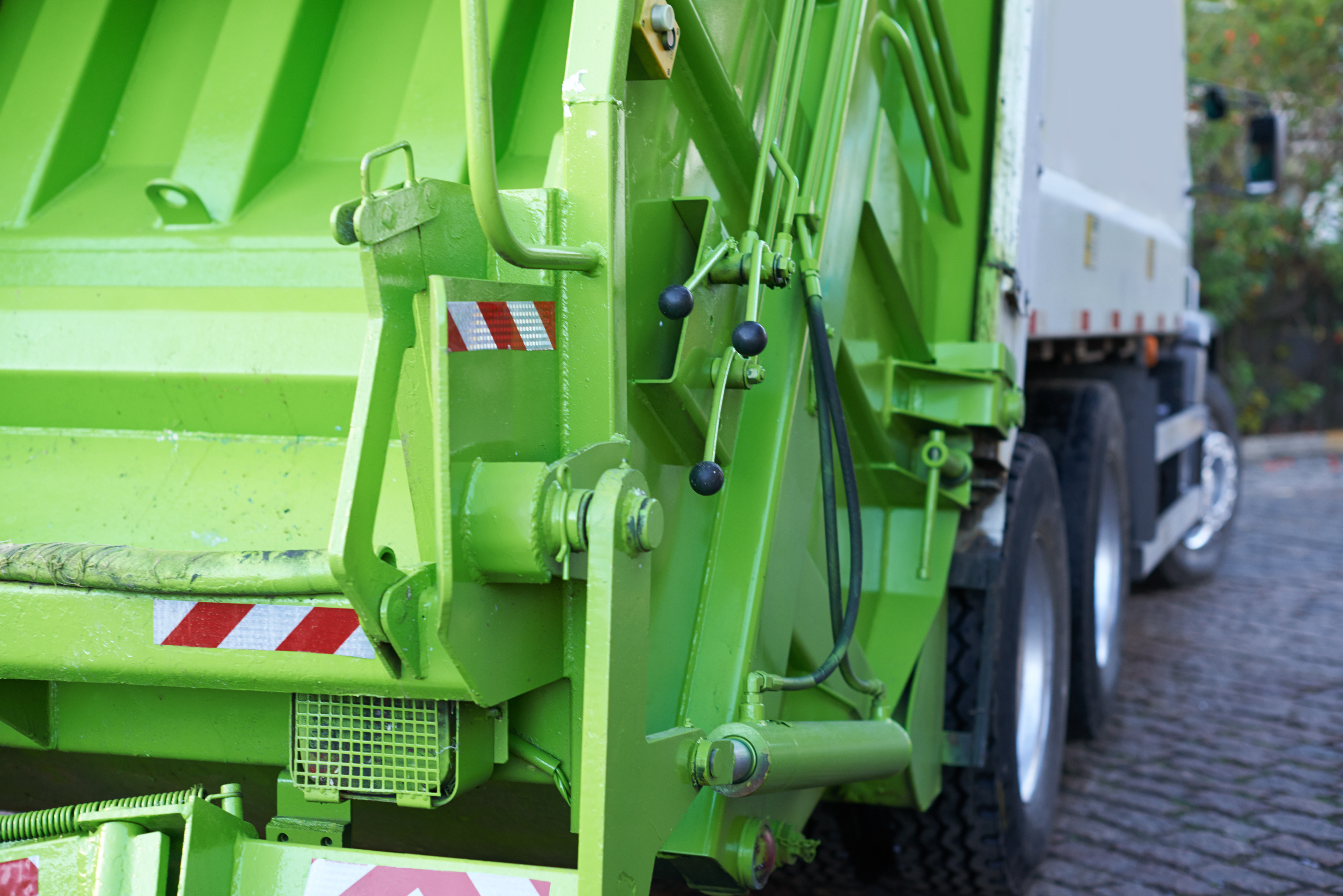